Friction Spot Joining
ENERGY SAVINGS FOR LIGHTWEIGHT ALLOY JOINING
The Kawasaki FSJ system has many benefits in comparison to spot welding for joining lightweight alloys. First, the system has low initial investment, 50% of a typical resistance spot welding (RSW) system, and there is no need for a water circulation system to cool the servo motor. Second, the FSJ process is highly energy efficient, requiring 5% of the energy in comparison to a resistance spot weld. Finally, the FSJ process does not result in fumes or material expulsion from the joined material.
Kawasaki can help you significantly reduce the cost of your lightweight alloy joining through the use of our innovative friction spot joining system.
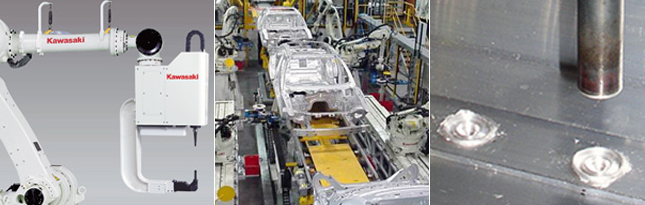
FRICTION SPOT WELDING ROBOTS:
Click on a robot below to learn more.
-
- ADVANCED FEATURES
-
- 5% energy consumption compared to RSW
- 50% initial investment compared to RSW
- Process controlled by Kawasaki controller
- Tooling life up to 1 million cycles
- No fumes or material expulsion
- Robot maintenance at 10,000 hour intervals
- Advanced joining depth control
- WHY KAWASAKI
-
- Industry leaders in FSJ robotic applications
- Pedestal or carried FSJ programming
- Turnkey custom FSJ systems
- Automotive friction spot joining experience
-
ADDITIONAL
RESOURCES